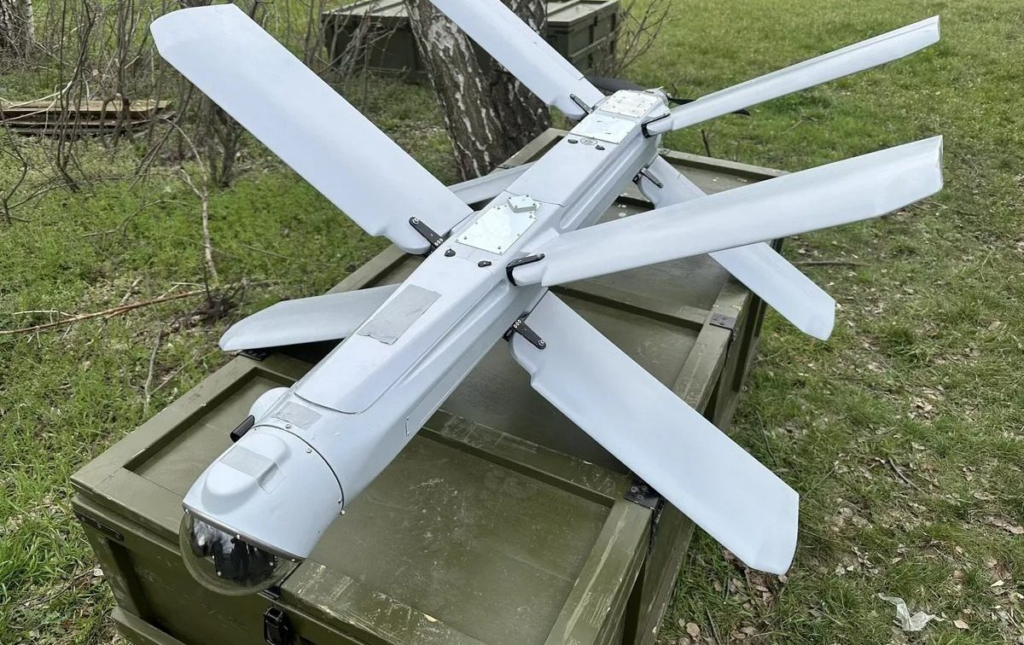
Continuing my exploration of Russian military hardware through the Ukrainian government’s open-sourcing of captured equipment, this time, it’s the turn of the much-feared Lancet drone. Unfortunately, however, unlike last time’s embezzlement project (the Supercam S350), the Lancet is both much cheaper and much more advanced. With the capability to fly in a circle above its target (loiter) for a long time, transmit video, and blow things up, this drone has become a feared symbol of how there are still some competent designers left in Russia. This article will use the following sources: https://war-sanctions.gur.gov.ua/en/components?f%5Bcountry_id%5D=&f%5Bmanufacturer_id%5D=&f%5Btitle_uk%5D=witem-odd-4266&f%5Bsearch%5D=&i%5Bmarking%5D=&page=2&per-page=12 (and all future Lancet drone teardowns released), https://mil.in.ua/uk/news/v-ukrayini-pokazaly-nachynku-trofejnogo-lantseta/.
In my opinion, there are five interesting and important features of this drone:
- The use of an Nvidia Jetson TX2 AI/computer vision module
- The use of an AMD/Xilinx Zynq XC7Z020 FPGA+MPU and camera system with an off-the-shelf industrial camera module (Skoopia 20Z10S-NF)
- The number of highly advanced Analog Devices data conversion and RF ICs (AD9364)
- The number of smaller microcontrollers in the drone:
- 1 STMicroelectronics STM32F103
- 2 NXP LPC2368
- 2 Microchip/Atmel ATMega8 and ATMega48
- The hobbyist sailplane motor (the Ukrainian government service presumes that it’s an AXI 4120, which is visually identical)
Let’s start in order.
Nvidia Jetson TX2
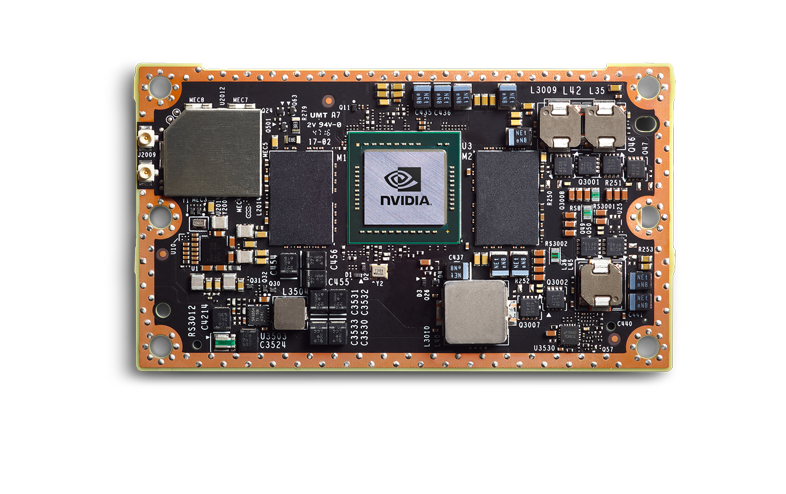
In the context of a drone that’s supposed to mark targets with computer vision and be able to track them for a long time, a Jetson TX2 is a very obvious choice. For 7.5W of power consumption, you get a 6-core MPU, a GPU, and 8GB of RAM. In terms of GPU power, you get approximately ⅔ the cores of an Nvidia GT1030 (256 cores), but Nvidia claims 2TFlops of single-precision float performance, which is on the level of a GTX1050. The GTX1050 may have been an entry-level gaming GPU at the time of its release, but it has much more processing power than you’d need for computer vision, which even a relatively fast ARM microcontroller can do. In terms of hardware, it’s practically identical to a Nintendo Switch. The performance is most likely very underutilized, but the module was likely chosen because it is an excellent development environment when compared to the effort needed to design a whole microcontroller board and optimize everything so that it runs properly. With a Jetson TX2, you’re a YouTube tutorial away from world-class, instant computer vision. The rapid development speed of the Lancet can very likely be significantly attributed to the relative simplicity of setting up computer vision on the Jetson TX2.
The camera and the AMD/Xilinx Zynq XC7Z020

There is not much to be said about the camera of the system, except for its curious similarity to the approximate market of the camera in the previously analyzed Supercam S350 drone. Both drones use commercial/industrial security cameras with decent optical zoom and stabilization. Both seem to have additional circuitry on them that basically acts as a remote control just so that they can put cheap civilian-grade equipment into a military drone. My critique of the S350’s camera applies here, which is just immense disappointment at how obviously rushed the design is. Nevertheless, their choice in commercial parts is actually pretty good (in commercial contexts) – at least this camera operates at high temperatures (unlike the S350’s).
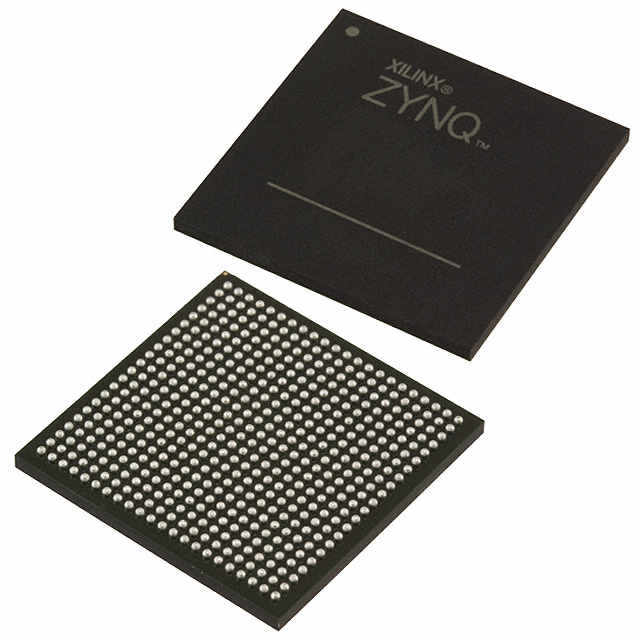
The AMD/Xilinx Zynq series of microprocessor + FPGA has been an absolute slam-dunk for the company. Being able to run Linux on one or two fast cores while offloading a ton of processing to the FPGA has made the Zynq series ubiquitous in measurement and industrial equipment. With their relatively low costs and power/board space efficiency, it’s no wonder that these found themselves used in the Lancet. However, I think that the Zynq’s addition to the system reveals a fundamental flaw with the architectural design of the Lancet that relates to the other sections – namely that the drone’s subsystems all have separate microcontrollers and microprocessors for everything, even though just having one of any of the three would likely be enough to get things working. The Zynq by itself has enough FPGA space to practically emulate all of the other microcontrollers and enough processing power to do image processing with some clever software. So what is the Zynq doing?
A clue lies in the fact that the Zynq is located on the Video Stream Processing Link board. The video stream from the camera is in the SDI (SMPTE 274M) format, which gets converted to an analog signal (in an ADV7391 video encoder) and transmitted downstream (with an AD9364). Simultaneously, the video stream from the ADV7391 is (presumably) converted to an MPU-compatible input with the ADV7180 video decoder. The ADV7391 is explicitly mentioned as being compatible and used with the ADV7180 in the latter’s datasheet. What is confusing to me is the obvious question of why they didn’t put all of this inside the Zynq? Video encoding/decoding is something that the Zynq is more than powerful enough for. Why have an FPGA if you’re going to use expensive (30$+ total for the encoder/decoder pair) ICs to do the conversion? Why have microprocessors if you’re going to use a Jetson TX2?
The data conversion and RF ICs
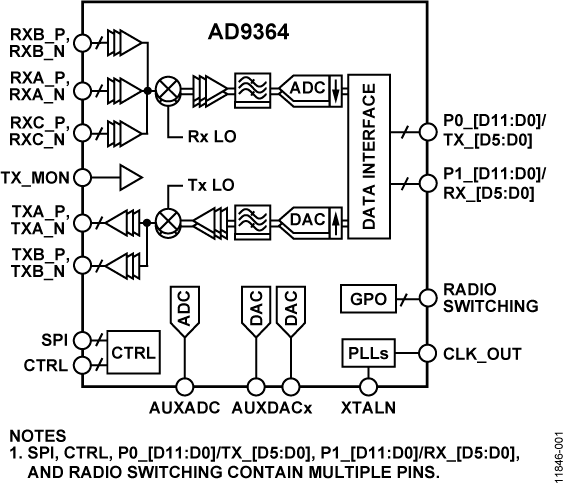
The previous section leads to this one, where the same question can be asked – why include an ethernet transceiver in the drone as well? The design seems needlessly overcomplicated and failure-prone. This is particularly strange when most of these ICs are dual-use, meaning that they should be even harder to get for a heavily sanctioned country. They should be minimizing the use of any of these, particularly when their domestic industry has nowhere near the capabilities of producing those ICs. If the source of one gets cut off, they’ll have to smuggle these strange, obscure ICs just to get the thing flying and working.
However, as I’ve often noticed with these Russian designs, their RF boards look excellent and well-designed. I wouldn’t be surprised if they’re reference designs, however. In the signal chains, you can find the usual RF amplifiers and the boards look relatively simple. Interestingly, the AD9364 RF transceiver used is meant for 3G and 4G base stations. However, the transceiver has amazing characteristics and a wide frequency range. This is probably what makes it well-suited for transmitting the analog video signals sent out by the camera with the overlays. You may note that practically all of these drones are built out of off-the-shelf commercial and industrial parts.
Also, the people responsible for analyzing the drone may not have noticed/known, but the connector for the RF transceiver board is a Samtec LSHM rugged board-to-board connector. I was looking at them for the new flight computer in my university rocketry club. They seem excellent. I was also looking at the AD9364 for the same purpose. Design convergence is a very real thing.
The smaller microcontrollers
What I somewhat like about the design is the use of smaller microcontrollers for very specific tasks whenever a bunch of analog circuitry would usually be needed. In the drone, four use cases of this are evident:
- A Microchip/Atmel ATMega8A is (presumably) used as a power supply monitor. It’s essentially a cut-down ATMega328 (of Arduino fame) with less memory but with the same number of analog inputs (6 channels, 10-bit). They have fast interrupt performance and use the excellent AVR instruction set. For a relatively simple system like this, they make for good power supply monitors.
- An NXP LPC2368 is used as the flight controller. This MCU is basically an Arm microprocessor with integrated RAM/flash. Funnily enough, this is also similar to a microcontroller used in a Nintendo console – the Nintendo Game Boy Advance. The core had amazing specs for when it came out; however, it was essentially obsolete in 2001. I’ve seen this MCU and similar ones from the family used in a lot of Russian military gear, so there may be a design legacy here. In any case, this MCU is built for DSP and algorithms, so flight control is something that it should be perfect at. It also interfaces with some sensors and serial converters (there’s also RS485 on the board for some reason – why do they have both that and ethernet? (one is likely for controlling the camera)).
- An STMicroelectronics STM32F103 is used for the “Optical rangefinder and warhead control unit (and gyroscope)”. I assume the STM32F103 was chosen here because of the rangefinder part duties, as it is also good at running algorithms. This board contains some huge transistors, as well as some direction and motion sensors. The STM32F103 should be well-suited to keep everything steady when it should be – and then suddenly make it unsteady.
- A Microchip/Atmel ATMega48V (also very similar to the Arduino) is used as the electric motor control unit. It’s an interesting choice for a motor controller, but a well-programmed control loop would likely run well – even despite the microcontroller being an 8-bit, FPU-less design.
The direction of separate microcontrollers for specific tasks is an interesting design choice – one that many complex designs have to make. Is it better to have one main processor/controller or have many small processors/controllers distributed throughout the system? The drastic processing power increases (with their corresponding power and space requirement decreases) in modern microcontrollers certainly make the choice easier, as it is easier than ever to have both. The Lancet’s designers seem to have taken this route; however, this opens up a vital question for the design: how much of a “black box” are all of the subsystems?
By this question, I mean the possibility of making subsystem-level architectural changes easily. Even though the current system has a ton of potential and processing power, the enormous variety of different microcontroller architectures and toolchains presents a complex architectural, design, and managerial task when making changes. This is where the obvious confidential nature of military designs is the biggest obstacle: we cannot see what is going on inside the meeting rooms and design bureaux of the Russian military-industrial complex. The questions to be asked here, from a lifecycle perspective, are:
- How easily can the system be changed?
- How many of the subsystems were (possibly internally) off-the-shelf?
- How much additional technical debt will the enormous number of toolchains add (AVR, STM, LPC, Xilinx FPGA, Zynq Linux, Nvidia Linux, Nvidia GPU)?
- Are the designs of the subsystems of the drone locked in place or changed as the drone develops?
- How much design overhead do the inter-processor communications add?
- How much space, weight, and power could be saved by consolidating the design?
- How long would it take to consolidate the design?
- Is there an ongoing effort to streamline the design?
- Can the drone’s subsystems be redesigned to use local components?
For question 8., there is a tentative answer in the Ukrainian website’s addition of a “Lancet-3” model, corroborated by Wikipedia and its sources. However, internally the design seems to be practically identical to the previous one, from what can be inferred from the limited information available.
The motor
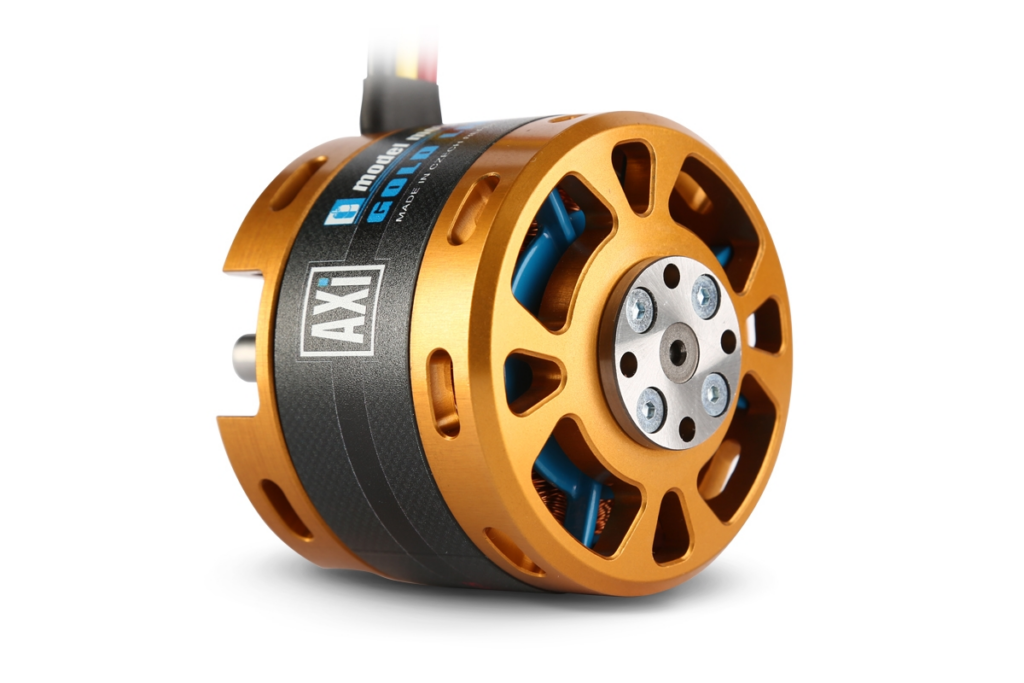
Question 9. from the previous section leads into the section on the motor with another curiosity – the motor used for the drone is (likely) a commercial AXI 4120 sailplane electric motor. It’s a simple, lightweight BLDC motor. Though it’s likely hard to obtain given all the sanctions, the Russian military has chosen the path of obtaining hobbyist motors, rather than building BLDC motors themselves. In the world of electronics, electromechanical parts are relatively easy to produce, but we’re not seeing much domestic manufacturing of those either. In fact, some other Russian gear that has even been recently built uses old-stock Ukrainian relays. Despite all of the macho posturing of the Russian military, the pictures of Soviet 1940s howitzers being pulled out of storage and shot until their rusted barrels explode support the story that they cannot make anything. The videos and articles published in the past 30 years of normal Russians scavenging extremely complex and expensive military equipment for milligrams of gold, silver, and palladium while the military literally uses washing-machine-grade parts support the story that they cannot make anything. Soviet designs from even 70 years ago were more advanced and more elegant than what they make now. All of this is pathetic and the lack of action by western politicians is pathetic. Send more money to Ukraine.
An addendum
I’d like to estimate the costs of the more expensive parts in the drone (at least for the more expensive ones) given current commercial prices:
- Jetson TX2 – 200 eur
- AMD/Xilinx Zynq XC7Z020 – 150 eur
- Camera – ~500 eur
- Motor – ~200 eur
- RF transceiver – ~250 eur
- Data conversion and RF ICs – ~100 eur
You can see that we’re already at ~1400 eur and that’s not even counting all of the components, circuit boards, batteries, connectors, antennas, and the drone’s frame. As the YouTuber Perun said in a recent analysis of Russia’s economy, it seems that most of the state-owned military-industrial companies are running on low margins, which would definitely be true for this drone. Adding import, software, development, testing, infrastructure, training, and auxiliary equipment costs likely mean that this drone is running either near zero or on a negative profit margin. The situation gets even worse when accounting for the markups of having to smuggle all of this equipment through neighboring countries.
If any company wants their name or image removed, contact me.